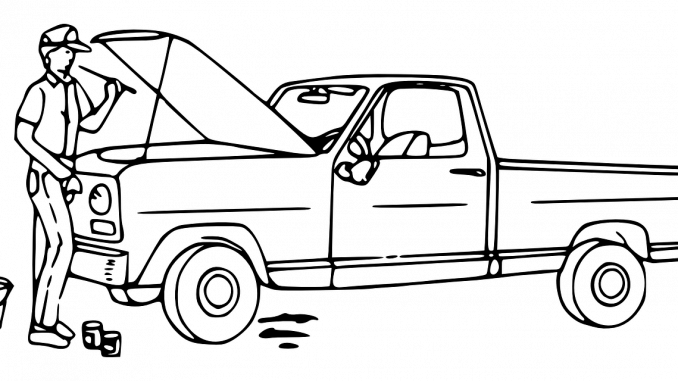
Managing downtime in manufacturing such as the food and biotechnology industries is crucial for maintaining efficiency, productivity, and profitability. Downtime can be caused by various factors, including equipment failures, maintenance activities, changeovers, and unexpected disruptions.
Planned downtime is needed by production to maintain machinery by conducting inspections, cleaning and replacing parts of the line. This should be built into the production schedule when the key properties of the line are put to one side whilst the planned downtime is implemented and all the operations needed are performed.
Contrast this then with unplanned downtime when equipment or parts of the process unexpectedly stop working. Equipment breakage, loss of power even to the toilets is enough to cause alarm and bring staff out of the workplace. Managed downtime is designed to prevent this sort of occurrence or at least put in place a contingency so that anything detrimental is minimised.
From the economics of the factory, its perspective is to minimise near-misses and accidents. In an unplanned stoppage, the goal is to have the machine up and running again as soon as possible. One of the consequences of unplanned failure in equipment is to create uncertainty with a loss of confidence in the equipment and the process.
There are number of strategies to help you manage downtime effectively and as with FoodWrite’s principles, we’ve listed them here.
- Predictive Maintenance
- Implement a predictive maintenance (proactive maintenance) program to anticipate and address potential equipment failures before they occur. The book by Levitt is worth perusing (Levitt, 2003).
- Use sensors and data analytics to monitor the condition of machinery and schedule maintenance based on actual usage rather than any fixed time intervals.
- Part replacement is also part of a scheduled maintenance where the key parts are ordered and available based on their rate of breakdown. A good rule of thumb is to have at least one easily replaceable part which is known to breakdown on a periodic basis rather than having a spare part for everything if it does not mean a complete shutdown of the plant.
- At least two or three suppliers should be known about for each piece of equipment.
- Regular Maintenance
- Establish a routine maintenance schedule for equipment to prevent breakdowns.
- Conduct preventive maintenance during planned downtimes to minimize the impact on production.
- Root Cause Analysis
- Investigate the root causes of downtime to address underlying issues systematically.
- Analyze historical downtime data to identify recurring problems and implement permanent solutions.
- A number of management systems exist to allow for straightforward interpretation.
- Employee Training:
- Train operators and maintenance personnel to identify early signs of equipment issues.
- Provide ongoing training to ensure that the workforce is equipped to handle routine maintenance and troubleshooting.
- Inventory Management:
- Maintain an adequate inventory of critical spare parts to minimize delays in equipment repairs.
- Partner with reliable suppliers to ensure a steady supply of necessary components.
- Equipment Upgrades and Modernization:
- Consider upgrading or replacing outdated equipment with more reliable and efficient technologies.
- Invest in automation to reduce the likelihood of human error and enhance overall efficiency.
- Real-time Monitoring and Alerts:
- Implement real-time monitoring systems to detect abnormalities in equipment performance.
- Set up automated alerts that notify maintenance personnel when issues are detected, allowing for a swift response.
- Downtime Tracking and Analysis:
- Use software and analytics tools to track and analyze downtime events.
- Categorize downtime events based on their causes to identify patterns and areas for improvement.
- This software needs to be easy to use and be jargon free. We’ve found that it has been implemented in the factory and no-one truly knows how to interpret the data or only understand a part of what the tracking is delivering.
- Ensure everyone being well versed in the application of statistics
- Cross-Training Employees:
- Cross-train employees to perform multiple roles within the production process.
- This ensures that there are individuals available to address issues even if specialized personnel are not present.
- Give them tools and troubleshooting guides which can be used as soon as an unplanned event occurs. It will help in the discovery of the root cause of the problem.
- Contingency Planning:
- Develop contingency plans for potential disruptions, such as backup systems or alternative production methods.
- Regularly review and update contingency plans based on changing circumstances.
- Continuous Improvement:
- Foster a culture of continuous improvement as part of a strategy of development where employees are encouraged to suggest and implement efficiency-enhancing ideas.
- Regularly review and update processes based on lessons learned from downtime events.
By combining even some of these strategies, manufacturers in whatever industrial environment can minimize downtime, improve overall equipment effectiveness (OEE), and enhance the resilience of their operations. Regularly reviewing and adapting these strategies based on performance data and feedback will contribute to ongoing success in managing downtime.
References
Levitt, J. (2003). Complete Guide to Preventive and Predictive Maintenance. Industrial Press Inc.
Leave a Reply