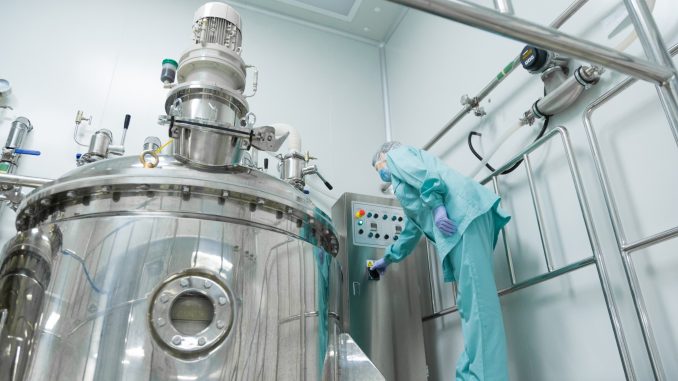
A single-use fermenter (SUF), also known as a disposable fermenter or single-use bioreactor, is a type of vessel used in biotechnology and bioprocessing industries for the fermentation of microorganisms, cells, or cultures to produce various products, such as pharmaceuticals, vaccines, enzymes, or biofuels. Unlike traditional stainless steel or glass fermenters, single-use fermenters are designed for one-time use and are then disposed of after a single batch or production run.
The SUF must also be designed to allow for the same high level of control as found in a permanent fermenter system.
Key features of single-use bioreactors/fermenters include the following:-
Materials
The single-use bioreactor is typically made from biocompatible and sterile plastic materials, such as polyethylene, polypropylene, or polycarbonate. These materials are chosen to ensure that the fermentation process remains contamination-free and to facilitate proper disposal after use.
Pre-sterilized
Single-use fermenters are delivered to the user pre-sterilized, eliminating the need for cleaning and sterilization before use. This feature saves time and resources in the production process.
Scalability
Single-use fermenters come in various sizes, ranging from a few liters to thousands of liters, allowing biotech companies to scale up or down their production as needed without investing in multiple traditional fermenters of different capacities.
Flexibility
They are designed to be compatible with various types of bioprocesses, including aerobic and anaerobic fermentation, microbial cultivation, and cell culture. Additionally, single-use fermenters can be equipped with sensors and controllers to monitor and control critical process parameters like pH, temperature, and dissolved oxygen.
Easy Disposal
Since single-use fermenters are used only once, there is no need for extensive cleaning and sterilization after the fermentation process. After use, they can be disposed of safely, reducing the risk of cross-contamination and ensuring a more straightforward waste management process.
Reduced Cross-contamination
By keeping the fermentation to a single-use only there is no subsequent risk to further batch fermentations.
Applications
The single-use bioreactor (SUB) has found increasing favour for cell culturing in recent years, mainly in mammalian cell culture but also for early-stage preparations of inocula, algae and other microbial processes (Hillig et al., 2014; Zhang et al., 2009). The SUB is generally taking over from conventional batch bioreactors.
When you consider the key features basic advantages are a reduction, even absence of microbial risk, a considerable lowering of operational costs because cleaning isn’t necessary, there is a short turn-around in replacement of units and relatively simple validation.
An SUB is typically made from polyethylene or polyester multi-layer films and foils and these are supplied, usually pre-sterilised by gamma irradiation (Singh, 1999). Three layers is common although many more might be used. Polyethylene terephthalate (PET) or low density polyethylene (LDPE) are prevalent and also provide some degree of mechanical stability. Barrier properties are provided by layers of polyvinylchloride (PVC) and/or polyvinylamide (PVA) which are commonly found in food barrier applications. Some bags are metallised to restrict light and provide other gas barrier properties. Stringent regulations define the contact materials used and each regulatory medical authority such as the European Medicines Agency will define this.
The bag is usually supported for rigidity and of glass or stainless steel. The working volume is extensive, from a range of 1 to 2,000 Litres (Brecht, 2009). There are a wide range of suppliers of such units and these can be readily sourced on the internet.
The main applications include early stage mammalian cell culture process development and inoculum generation (Kalmbach et al., 2011; Oncül et al., 2009) at scales up to 500 L. The original SUBs worked on a slowly rocked platform designed to induce a wave-type motion in the culture fluid promoting good mixing and gas mass transfer. They were described by colleagues as a plastic bag on a wave machine but minimised shearing of the cells. The Wave™ bioreactor relies on this principle of rocking motion (Wave Bioreactor, 2007).
The most recent SUB designs now resemble conventional stirred tank bioreactors and are now commonly used for therapeutic antibody and vaccine production up to 2000 L scale. In this design, the stirrer is incorporated into the bag and pre-sterilised too. The stirrer is then mechanically connected to a shaft or moved magnetically. This represents an advance on the wave motion approach to stirring although possible shear means it is intrinsically less gentle.
Issues with single-use bioreactors
One of the principal issues that the SUB suffers is overcoming the restriction of poor oxygen gas transfer. Design and construction constraints mean that insufficient power input is possible to improve both mixing and ultimately gas mass transfer. As with all reactors, when cell densities become high, very often oxygen mass transfer becomes limiting and the cells suffer stress. The reactor then becomes one for perfusion only.
Likewise, carbon dioxide removal is hindered to the same extent and can be an even bigger problem for extending the culture. This gas drops the pH of the medium by formation of carbonic acid. A slight acidification can be sufficiently deleterious on the performance of the bioreactor. To counter this, the pH must be raised which entails the use of buffering salts that might just for instance, raise salinity if sodium salts (Na+) are used.
A reactor which overcomes a number of limitation above is the CELL-tainer® single-use bioreactor. It not only supports higher cell densities than was possible before but also supports perfusion too.
Measurement and Control
Measurement and control is still feasible using conventional pH and dissolved oxygen probes even though the bag itself operates as a closed, pre-sterilised system. A variety of sensors based on patches, light probes etc. are available however and can be built into the bag and connected prior to use.
It would be interesting to know if there are any food uses that such a system might be put to use. The production of stomach related microbial products might be of interest.
Producers of Single-Use Fermenters
Thermo Fischer Scientific have developed the HyPerforma Single-Use Fermenter (SUF). The marketing story is primarily around an engineered system for optimal oxygen mass transfer, suitable mixing and temperature control. The unit comes in two sizes, 30 litres and 300 litres. It is a fermenter tank with a standard Thermo Scientific HyPerforma S.U.F. BioProcess Container (BPC). The BioProcess container also comes in a form ready for centrifuging. Again, this is a single-use, sterilized and closed system designed for cell harvesting. These SUB BioProcess containers fit into the bioreactor’s existing hardware. They are supplied sterile and ready-to-use, and come complete with a impeller, assembly spargers, vent filters, sensor ports and sensors with line sets for media, supplement sna dfor harvesting. One of the main selling points is the design of a single-use impellar with a bearing and seal assembly to couple directly to their external mixer drive.
The brand also supplies 5:1 turndown ratio vessels. These are operated in low-, half- and full-volume mixing. There are fewer seed train vessels with an ability to do cell runs in parallel vessels.
Eppendorf have created the BioBLU® c Single-Use Bioreactor which like many of its competitors uses monolayer virgin plastic with a rigid wall stirred-tank design to mimic conventional bioreactors. A wide range of sizes are available including 300 mL designed for cell culture, incorporating a 1 pitched-blade impellar. Larger sizes of 1 litre and 3 litres are available and include multi-bladed impellars. These bioreactors are designed for animal, plant and insect cell line culturing.
References
Brecht, R., (2009) Disposable bioreactors: maturation into pharmaceutical glycoprotein manufacturing. Adv. Biochem. Eng. Biotechnol. 115, pp. 1–31. http://dx.doi.org/10.1007/10.
Hillig, F., Porscha, N., Junne, S., Neubauer, P. (2014) Growth and docosahexaenoic acid production performance of the heterotrophic marine microalgae Crypthecodinium cohnii in the wave-mixed single-use reactor CELL-tainer. Eng. Life Sci. 14, pp. 254–263. http://dx.doi.org/10.1002/elsc.201400010.
Kalmbach, A., Bordás, R., Oncül, A.A., Thévenin, D., Genzel, Y., Reichl, U., (2011) Experimental characterization of flow conditions in 2- and 20-L bioreactors with wave-induced motion. Biotechnol. Prog. 27, pp. 402–409. http://dx.doi.org/10.1002/btpr.516.
Oncül, A.A., Kalmbach, A., Genzel, Y., Reichl, U., Thévenin, D., 2009. Characterization of flow conditions in 2 L and 20 L wave bioreactors using computational fluid dynamics. Biotechnol. Prog. 26, pp. 101–110. http://dx.doi.org/10.1002/btpr.312.
Singh, V., 1999. Disposable bioreactor for cell culture using wave-induced agitation. Cytotechnology 30, pp. 149–158. http://dx.doi.org/10.1023/A:1008025016272.
Wave Bioreactor: Nonproprietary Literature. Wave Biotech LLC: Somerset, NJ, (2007) www.wavebiotech.com/products/wave_bioreactor/literature.html
Zhang, Q., Yong, Y., Mao, Z.-S., Yang, C., Zhao, C. (2009) Experimental determination and numerical simulation of mixing time in a gas–liquid stirred tank. Chem. Eng. Sci. 64, pp. 2926–2933 http://dx.doi.org/10.1016/j.ces.2009.03.030.
Leave a Reply