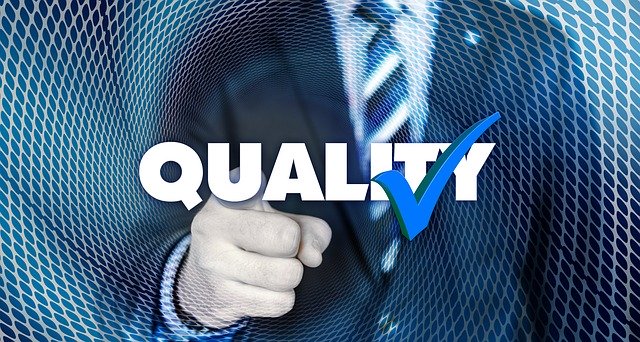
Introduction
Quality by Design (QbD) is a systematic and science-driven approach to pharmaceutical development that has transformed the landscape of drug manufacturing and product quality. This essay explores the principles of Quality by Design, its key components, and its impact on the pharmaceutical industry. From its inception to its current applications, QbD has become a cornerstone in ensuring the safety, efficacy, and quality of pharmaceutical products.
Quality is now formalised in most manufacturing circles under the mantra:-
“Quality cannot be tested into products; it has to be built in by design”. This statement led to a definition of what is ‘Quality By Design’. It is formally a:-
‘systematic approach to development that begins with predefined objectives and emphasises product and process understanding and process control, based on sound science and quality risk management’.
Concepts And Development Of Quality By Design (QBD)
Quality by Design is a concept first outlined by Joseph M. Juran in various publications. He supposed that quality could be planned. The concept of QBD was mention in ICH Q8 guidelines, which states that, “To identify quality can not be tested in products, i.e. Quality should be built in to product by design.”
The Benefits And Advantages Of QBD In A Nutshell
- Better understanding of the process
- Reduced batch failure
- More efficient and effective control of change
- More effective return on investment and cost savings.
- Reduction of post-approval submissions (especially pertinent in the pharmaceutical industry).
- Risk-based approach and identification
- Innovative process validation approaches.
Objectives Of QBD
The main objectives of QBD is to ensure the quality products, for that product and process characteristics important to desired performance must be resulting from a combination of prior knowledge and new estimation during development.
From this knowledge and data process measurement and desired attributes may be constructed.
Ensures combination of product & process knowledge gained during development.
Understanding Quality by Design
1. Definition and Evolution: Quality by Design is a holistic approach that integrates quality into the development and manufacturing processes of pharmaceutical products from the outset. It represents a departure from traditional trial-and-error methods, emphasizing a proactive and science-based strategy to ensure product quality. The concept of QbD gained prominence with the publication of the International Conference on Harmonisation (ICH) Q8, Q9, and Q10 guidelines, laying the foundation for its implementation across the pharmaceutical industry.
2. Key Components of Quality by Design:
2.1 Design Space:
- One of the central tenets of QbD is the concept of the design space. This refers to the multidimensional combination and interaction of input variables (e.g., raw materials, process parameters) and their effect on product attributes. By defining a design space, manufacturers can ensure product quality within specified ranges, providing flexibility in the manufacturing process without compromising safety and efficacy.
2.2 Risk Assessment:
- QbD employs risk assessment methodologies to identify and prioritize potential risks associated with product quality. This proactive approach allows manufacturers to mitigate risks early in the development process, enhancing the overall robustness of the product and manufacturing process.
2.3 Control Strategy:
- The control strategy in QbD involves establishing controls and specifications for critical quality attributes (CQAs) and critical process parameters (CPPs). This ensures that the manufacturing process consistently produces a product meeting the desired quality attributes. Real-time monitoring and feedback mechanisms are integral to the control strategy.
2.4 Continuous Improvement:
- Continuous improvement is ingrained in the QbD framework. Through the use of statistical tools, ongoing monitoring, and feedback loops, manufacturers can identify opportunities for improvement, optimizing processes and enhancing product quality over time.
Applications of Quality by Design:
1. Drug Development:
- QbD has revolutionized the drug development process by emphasizing a more comprehensive understanding of the relationships between formulation, process parameters, and product attributes. This approach expedites the identification of optimal conditions and facilitates a smoother transition from development to commercial production.
2. Process Analytical Technology (PAT):
- PAT is a key enabler of QbD, allowing for real-time monitoring and control of critical process parameters. Technologies such as spectroscopy, chromatography, and sensors provide valuable insights into the manufacturing process, enabling timely adjustments and ensuring consistency in product quality.
3. Regulatory Compliance:
- Regulatory agencies, including the U.S. Food and Drug Administration (FDA) and the European Medicines Agency (EMA), endorse and encourage the adoption of QbD principles. A QbD approach facilitates regulatory submissions by providing a clear understanding of the manufacturing process, design space, and control strategies, thereby expediting regulatory approvals.
4. Life Cycle Management:
- QbD extends beyond initial product development and plays a vital role in the life cycle management of pharmaceutical products. As technologies evolve and new information emerges, QbD allows for the continuous improvement of processes, ensuring that products maintain their quality and remain in compliance with regulatory standards.
Challenges and Criticisms:
1. Implementation Costs:
- One of the challenges associated with QbD is the initial investment required for the implementation of advanced technologies and training of personnel. However, proponents argue that the long-term benefits, including reduced variability and increased process efficiency, outweigh the initial costs.
2. Cultural Shift:
- Implementing a QbD approach often necessitates a cultural shift within an organization. This involves fostering a mindset that prioritizes continuous improvement, embraces risk assessment, and values the systematic understanding of the product and its manufacturing processes.
3. Complexity of Implementation:
- Some critics argue that QbD, with its emphasis on detailed process understanding and sophisticated statistical tools, can be complex to implement, especially for smaller companies with limited resources. However, proponents assert that the scalable nature of QbD allows for adaptation based on the complexity of the product and process.
Future Directions and Innovations:
1. Advanced Analytics and Machine Learning:
- The integration of advanced analytics and machine learning into QbD holds promise for enhancing predictive modeling and optimizing manufacturing processes. These technologies can analyze vast datasets, identify patterns, and contribute to a deeper understanding of complex interactions within the design space.
2. Personalized Medicine:
- As the field of personalized medicine advances, QbD principles can be applied to tailor drug formulations and manufacturing processes to individual patient needs. This individualization ensures that products are not only safe and effective but also optimized for specific patient populations.
3. Integration with Industry 4.0:
- Industry 4.0, characterized by the integration of smart technologies and the Internet of Things (IoT) into manufacturing processes, aligns well with QbD principles. Real-time data collection, connectivity, and smart sensors can enhance the agility and responsiveness of manufacturing systems, facilitating QbD implementation.
Conclusion
Quality by Design has emerged as a transformative approach in pharmaceutical development, aligning with the industry’s goals of ensuring product quality, safety, and efficacy. Its holistic framework, encompassing the design space, risk assessment, control strategies, and continuous improvement, has reshaped how pharmaceutical products are developed, manufactured, and maintained throughout their life cycle.
While challenges exist, including implementation costs and the need for a cultural shift, the benefits of QbD in terms of regulatory compliance, enhanced predictability, and continuous improvement outweigh these concerns. As technologies continue to advance, and the pharmaceutical industry embraces concepts such as personalized medicine and Industry 4.0, the principles of Quality by Design will likely play an increasingly pivotal role in shaping the future of pharmaceutical manufacturing and drug development.
Leave a Reply